-
Prospective Students
-
Current Students
-
Faculties
-
Maritime Sciences
-
Social Work and Health
- Insight the Faculty
- Contact
- Erstsemesterinformationen
- International
-
Forschung
- Institute
- Laboratory
-
Projects
- COVID
- EBBiK - Entwicklung von Bildfähigkeit als Bildungsauftrag
- Familienzentrum Aurich (FamZ)
- Kombi-Nord
- Kommunale Suchtprävention in der Satdt Delmenhorst
- Kommunales Teilhabekonzept für die Stadt Emden
- REFU
- Sociotechnical Practices of Objectivation
- SoWeKi
- Suchtpräventionskonzept des Landes Niedersachsen
- Suchtprävention in Schulen (SiS)
- Wer nicht fragt, geht offline: Kids as digital citizens
- Werkstatt für Praxisforschung
- WOGO
- WOGE
-
Team
- Hilfen zum Studium
- Praxisreferat
-
Study Programs Social Work and Health
-
Technology
- Current topics
- Contact
- Study
- Research
-
Projects
-
Laboratories
- Additive Fertigung
- Denkraum
- Designlabor
- FabLab - Labor für studentische Projekte
- Automation Systems
- Bioverfahrenstechnik
- Biochemie/Molekulare Genetik
- Innovationen im Ingenieurwesen
- Instrumentelle Analytik
- Intelligente Produktionssysteme
- Kolbenmaschinen
- Machine dynamics
- Leichtbaulabor
- Maschinenelemente
- Mechatronik
- Mikrobiologie
- Organische Chemie/Nachwachsende Rohstoffe
- Physikalische Chemie
- Polymere
- Lab for production planning
- Produktionstechnik
- Networked Systems
- Regelungstechnik
- Labor S4
- Technische Informatik
- Verfahrenstechnik
- Werkstoffkunde, Laser- und Fügetechnik
- wind energy lab
- Zellkulturtechnik
- Research / Institutes
- Insight the Faculty
-
Study Programs
- Applied Life Sciences (Master)
- Biotechnology
- Biotechnologie im Praxisverbund
- Business Intelligence and Data Analytics
- Chemical Engineering/Environmental Technology
- Chemietechnik im Praxisverbund
- Electrical Engineering
- Electrical Engineering (Dual Study)
- Engineering Physics
- Engineering Physics (Master)
- Renewable Energy and Energy Efficiency
- Industrial Informatics (Master)
- Computer Science
- Computer Science (Dual Study)
- Mechanical Engineering and Industrial Design
- Mechanical Engineering and Industrial Design (dual degree course)
- Mechanical Engineering (Master)
- Medieninformatik (Online)
- Medieninformatik (Online, Master)
- Media Technology
- New study program page NaPriMa
- Nachhaltige Prozesstechnologie
- Nachhaltige Prozesstechnologie (PV)
- Wirtschaftsinformatik (Online)
- Regenerative Energien (Online)
- Technical Management
- Technology of Circular Economy
- Computer Science and Economics
- Wirtschaftsingenieurwesen – Engineering & Management
-
Business Studies
- Module manuals, regulations & preliminary work
- News, dates & information about the current semester
- Projects & Research
-
Courses of studies
- Business Management (M. A.)
- Energy & Sustainability Management (B. Sc.)
- Digital Management (B. Sc.)
- Business Management - BWL (B. A.)
- International Business & Culture (B. A.)
- Betriebswirtschaft dual (B.A.)
- Business Studies (B. A.)
- business psychology
- International Business Administration (B.A. )
- Advanced Management berufsbegleitend (M. Sc.)
- Advanced Management Stipendium
- Management Consulting (M.A.)
- Business Informatics (Online)
- Team
- Before your studies
- Graduates & Alumni
- In studies
- Information for schools
-
Maritime Sciences
- Studium
- Services
- International campus
-
Life on campus
-
Faculties
-
QuickLinks
-
University of Applied Sciences
-
Für Unternehmen
-
Centre for further education
- Übersicht
-
Weiterbildungen
- Burnout-Prophylaxe
- Cybercrime
- Gamification für Businesstransformation
- Business Basics for School
- Sustain 2030
- Lean Management
- „Nordbeat–der Norden macht Zukunft:Tag der Weiterbildung
- Business 2 Business - 5.0
- Betrieblicher Gesundheitsmanager in BPS
- Programmieren mit Scratch
- Cyber-Security Hacking Training
- Konfiguration mit Sidekick -Humanisierung der KI
- Kommunikation, Wertschätzung und Selbstmanagement
- Konflikt-Kommunikation
- Kommunikation und Gesprächsführung:Konflikt-Kommunikation
- Kommunikation & Zusammenarbeit
- Humor in der Beratung
- Kundenzentrierung-Customer Centricity für KMU & Start-UP
- Nachhaltigkeitsberichterstattung
- Gewaltfreie Kommunikation
- Casemanagement im Praxisalltag
- Trauma-Pädagogik
- Reflexionstag
- Outdoor-Erlebnis
- Finance for non-finance
- Management-Essentials: Gamification für BWL-Einsteigende
- Marketing Praxiswerkstatt
- Software Development
- Nachhaltige Führungskräfteentwicklung
- Einführung in die Produktionstechnologie
- Traumaberatung
- Systemische Beratung und Coaching
- Windenergie-Nutzung
- The region in focus
- press
-
Organization
-
Departments A-Z
- Workplace Safety
-
University Library
-
CampusDidaktik
- Team CampusDidaktik
- Q&A
- Positionspapiere
- Tools für Lehre und Zusammenarbeit
- Moodle
- Impulse und Inspiration für die Lehre
- Kleingruppenarbeit begleiten
- Urheberrecht in der Lehre
- KI in der Hochschullehre
- Hybride Lehre
- Barrierefreiheit in der Lehre
- Planspielzentrum
- Digitale Prüfungen
- Ipro-L
- Didaktische Beratung
- Career Service
- Datenschutz
- Finanzabteilung
- Gebäudemanagement
-
Gleichstellungsstelle
- Planning and Quality Assurance
- health & sports
-
Admission and Examination Office
-
International Office
- Your way abroad
-
International Students
- German Classes
- FAQ incoming students
- degree-seeking students
- Exchange Students / ERASMUS+
- Housing
- Buddy-Program for International Students
- International Sustainability Program
- Living Expenses
- Scholarships
- Visa
- Health Insurance and Co.
- Studying with Impairment (Inclusion and Accessibility)
- Internships & Jobmarket
- Event notes
- Internationalization at home university
- Partner Universities
- Staff Mobility
- Contact & Download Area
- Allgemeines über ERASMUS+ Programm
- Kommunikation und Hochschulkultur
- MeerCommunity Startup Center
-
Sustainability
- Ombudswesen
-
Personalabteilung
- Staff Council
- Präsidialbüro/Presse- und Öffentlichkeitsarbeit
- Computer Center
- Language Centre
- Studium Generale
- MyCampus
- [Translate to english:] Operating group ver.di
- Wissens- und Technologietransfer
-
Student Counselling Service
- Zentrum für Weiterbildung
- Karriere
- Administration
- Events
- Mission statement
- Organizational chart
- Figures, data and facts
-
Regulations, guidelines and announcements
- Regulations and rules
-
Ordnungen für Studiengänge
- Advanced Management
- Applied Life Sciences
- Betriebswirtschaft
- Betriebswirtschaft (dual)
- Biotechnologie/Bioinformatik
- Biotechnologie
- Biotechnologie im Praxisverbund
- Business Administration (dual)
- Business Intelligence and Data Analytics
- Business Management
- Business Management (Bachelor)
- Chemietechnik/Umwelttechnik
- Chemietechnik im Praxisverbund
- Digital Management
- Elektrotechnik
- Elektrotechnik im Praxisverbund
- Elektrotechnik und Automatisierungstechnik
- Energieeffizienz
- Energy and Sustainability Management
- Engineering Physics (Bachelor)
- Engineering Physics im Praxisverbund
- Engineering Physics (Master)
- Erneuerbare Energien und Energieeffizienz
- Industrial Informatics
- Informatik
- Informatik im Praxisverbund
- Inklusive Frühpädagogik
- Interdisziplinäre Physiotherapie/Motologie/Ergotherapie
- International Business Administration
- Internationaler Studiengang Wirtschaftsingenieurwesen (IBS)
- International Business and Culture
- Kindheitspädagogik
- Lasertechnik
- Management Consulting
- Maritime Operations
- Maritime Technology and Shipping Management
- Maschinenbau
- Maschinenbau und Design
- Maschinenbau und Design für Berufsqualifizierte
- Maschinenbau und Design im Praxisverbund
- Medientechnik
- Nachhaltige Produktentwicklung im Maschinenbau
- Nachhaltige Prozesstechnologie
- Nachhaltige Prozesstechnologie im Praxisverbund
- Nautik
- Nautik und Seeverkehr
- Online-Bachelorstudiengang Medieninformatik (Voll-/Teilzeit)
- Online-Masterstudiengang Medieninformatik (Voll-/Teilzeit)
- Online-Bachelorstudiengang Regenerative Energien
- Online-Bachelorstudiengang Wirtschaftsinformatik (Voll-/Teilzeit)
- Online-Masterstudiengang Wirtschaftsinformatik
- Physiotherapie
- Schiffs- und Reedereimanagement
- Soziale Arbeit
- Soziale Arbeit (BASA-online)
- Soziale Arbeit und Gesundheit im Kontext sozialer Kohäsion (Vollzeit/Teilzeit)
- Soziale Kohäsion im Kontext Sozialer Arbeit u. Gesundheit
- Sozial- und Gesundheitsmanagement
- Sozialmanagement
- Sustainable Energy Systems
- Technical Management
- Technology of Circular Economy
- Wirtschaftsinformatik (Dual)
- Wirtschaftsingenieurwesen Maritime Wissenschaften (B.Sc.)
- Wirtschaftsingenieurwesen - Engineering & Management
- Wirtschaftspsychologie
- Verkündungsblätter
- Committees
- University representatives
- University elections
-
Departments A-Z
- Study locations
-
Für Unternehmen
-
Research
-
Focuses
- Research strategy
- Forschungsschwerpunkte
-
Forschende
- Seefahrt und Maritime Wissenschaften
- Soziale Arbeit und Gesundheit
-
Wirtschaft
- Prof. Dr. Knut Henkel
- Prof. Dr. Tom Koch
- Prof Dr. Ute Gündling
- Prof Dr. Annika Wolf
- Prof. Dr. Jan Handzlik
- Prof. Dr. Hans-Gert Vogel
- Prof. Dr. Till Becker
- Prof. Dr. Henning Hummels
- Prof. Dr. Thomas Lenz
- Prof. Dr. Wolfgang Portisch
- Prof. Dr. Jan Christopher Pries
- Prof. Dr. Ute Rademacher
- Prof. Dr. Marco Rimkus
- Prof. Dr. Eva-Maria Schön
- Prof. Dr. Joachim Schwarz
- Technik - Elektrotechnik + Informatik
- Technik - Maschinenbau
-
Technik - Naturwissenschaftliche Technik
- Prof. Dr. Gerhard Illing
- Prof. Dr. Gottfried Walker
- Prof. Dr. Ingo de Vries
- Prof. Dr. Mark Rüsch gen. Klaas
- Prof. Dr. Jens Hüppmeier
- Prof. Dr. Iván Herráez
- Prof. Dr. Ralf Habermann
- Dr. Julia Jessica Reimer
- Prof. Dr. Claudia Gallert
- Prof. Dr.-Ing. Philipp Huke
- Prof. Dr. Martin Silies
- Prof. Dr. Martin Sohn
- Prof. Dr. Sven Steinigeweg
- Prof. Dr. habil. Ulrich Teubner
- Folgeabschätzung und Ethik
- Promotionen
- Leitbild Existenzgründung
-
Projects
-
Aktuelle Projekte
- Adaptive Fortbildungen in der medienpädagogischen Altenbi
- AnkerPROF
- Biotech Talent Unlocked
- BUFFER+
- CargoTube operation facility
- CROSSLOG
- EARLY
- Entwicklung eines Reinigungsroboters für Offshore-WKA
- ExStyrol
- FlettnerFLEET
- GE-VORS
- GG-Check
- HyLab
- Hyper4Rail
- InnoWerft
- Integrierte und innovative maritime Technologien für Mobi
- Kipti
- MAVERIC 5G
- Meer-O - Mehr Entrepreneurinnen für Emden und die Region
- MIINTER
- NESSIE
- Nordwest Niedersachsen Nachhaltig Neu (4N)
- PANTHER
- Professorinnenprogramm III
- ProlOg
- RASANT
- ReqET
- SIoT-Gateway
- SoWeKi
- StaKiNd
- Standardisierung, Weiterentwicklung und Kommunikation von
- tubLANQ.0
- Transferzentrum für Nachhaltige Mobilität
- TwinMaP
- Wind & Regio
- W4S - Wind4Shipping
- WaddenVision
- Wissenschaftliche Begleitung Strukturwandel Ostfriesland
- Zukunftslabor Produktion
- Projekte nach Bereichen
- Beendete Projekte
-
Aktuelle Projekte
-
Research institutes
- Promotionskollegien
-
Institute
-
Netzwerke
- Nationalpark Wattenmeer
- Promotionsnetzwerk Emden/Leer
- Digital Hub Ostfriesland (DHO)
- Tötungshandlungen in Einrichtungen des Gesundheitswesens
- Wachstumsregion Emsachse
- Maritimes Kompetenzzentrum (Mariko)
- greentech Ostfriesland
- NorShiP-Research School
- Association of Schools of Public Health
- Hochschulen für Gesundheit
- Deutsche Gesellschaft für Public Health
- Powerhouse Nord
- GENDERnet
- Einrichtungen in den Fachbereichen
-
Advice
-
Focuses
You are here:
- University of Applied Sciences Emden/Leer
- Current Students
- Faculties
- Technology
- Laboratories
- Machine dynamics
- Projektübersicht
- Dynamische Stangendichtungen (DFG Einzelförderung)
1. Container Projekte
FEM-Simulation einer gedruckten Stangendichtung
1. Step: Einpressvorgang einer gedruckten Stangendichtung

Die Nutgröße wird zunächst als "zu groß" modelliert. In einem zeitabhängigen Berechnungsschritt werden Stangen - und Nutdurchmesser geometrisch korrigiert. Durch Einführung von Kontaktbedingungen wird die Dichtung zusammengepresst. Da es während des Zusammenpressens zu starken Netzverformungen kommt, müssen während der Berechnung divere Remeshing-Steps durchgeführt werden.
2. Step: Erhöhung der Stangengeschwindigkeit
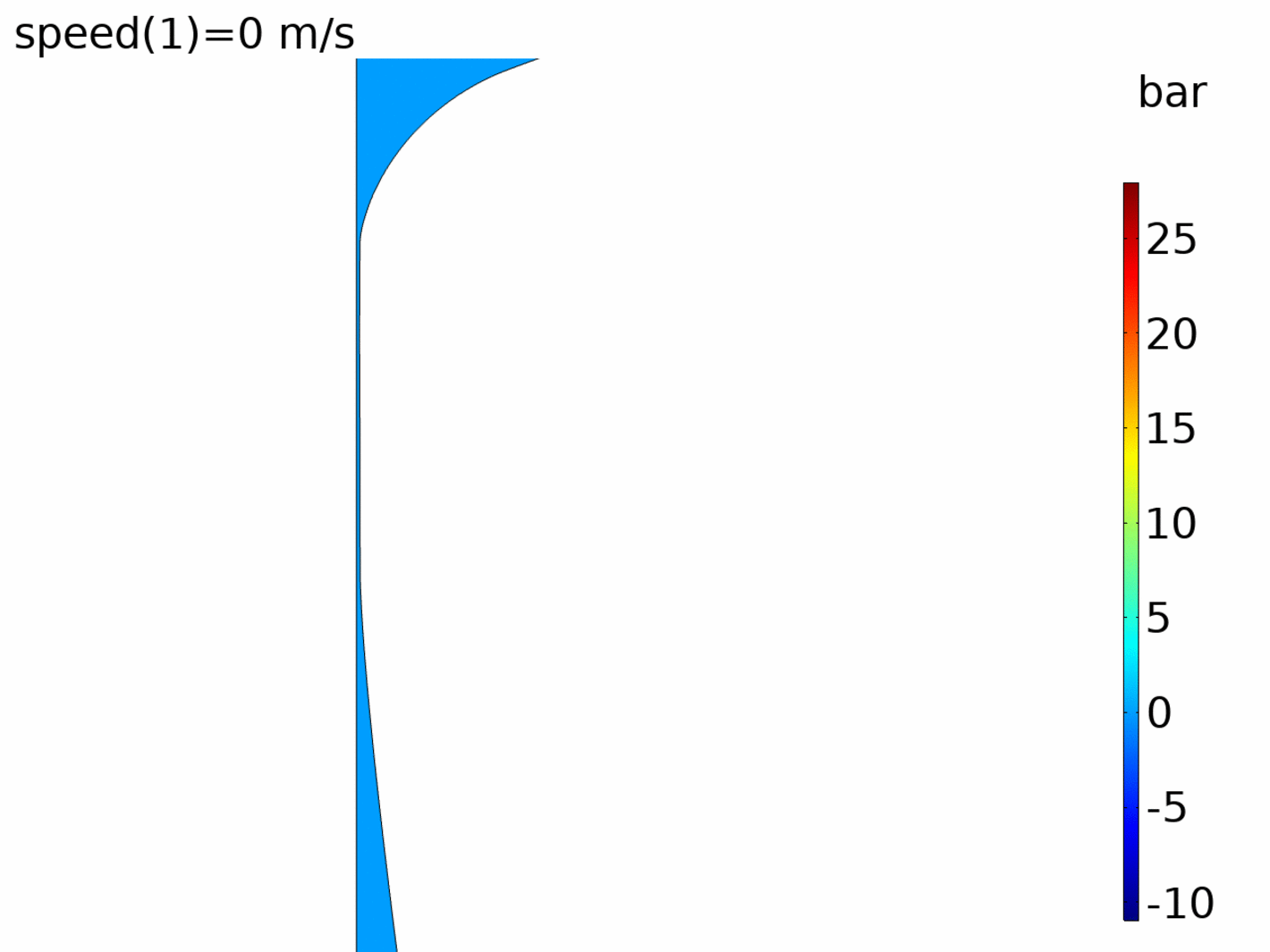
Zu sehen ist eine vergrößerte Ansicht der linken Dichtlippe. Die am linken Bildrand dargestellte Stange bewegt sich nach oben und die Geschwindigkeit wird schrittweise erhöht. Durch die Erhöhung der Stangengeschwindigkeit wird das Fluid in den Dichtspalt gedrückt. Infolge dessen steigt der Fluiddruck und die Dichtung wird durch die Fluid-Struktur-Interaktion verformt.
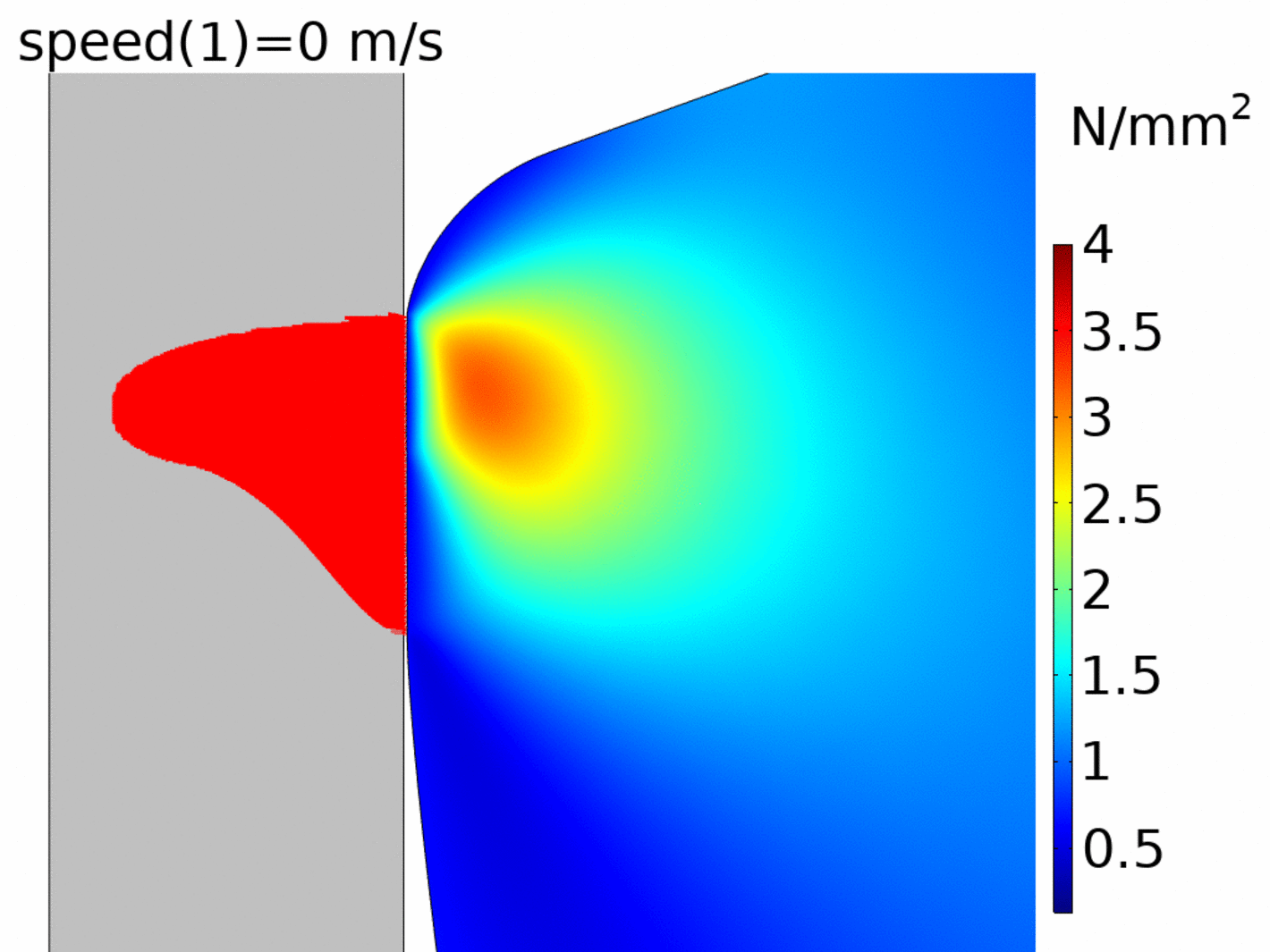
schwarz: Fluidkraft infolge der Stangenbewegung
Durch die Erhöhung der Stangengeschwindigkeit steigt der Fluiddruck (schwarz) stetig an. Bei ca. 1,7 m/s ist die Kontaktkraft (rot) null und die gesamte Kraft wird durch das Fluid getragen. Es handelt sich hierbei nicht um ein Kräftegleichgewicht, da nach Elimierung der Kontaktkraft die Fluidkraft weiter ansteigt.
Dynamische Stangendichtungen (DFG Einzelförderung)
Dynamische 2-Komponenten-Dichtungen aus additiver Fertigung: DFG Einzelförderung 2021-2024
Auf Offshore-Plattformen oder anderen, abgelegenen, Orten schnell Ersatzdichtungen mit dem 3D-Drucker herstellen, z.B. für Windkraftanlagen: dies soll durch ein Projekt ermöglicht werden, dass die Deutsche Forschungsgemeinschaft fördert. Ziel des Vorhabens ist es, in nur einem Fertigungsschritt die Produktion zweier Kunststoffteile und ihre Kombination zu einer einsatztauglichen Dichtung zu vereinen.
Projektpartner des Labors für Maschinendynamik sind das Labor für additive Fertigung der Hochschule Emden/Leer und das Deutsche Institut für Kautschutechnologie e.V.
Konkret geht es um die Entwicklung und Herstellung dynamischer Stangendichtungen aus zwei Komponenten aus einem Elastomer und einem Thermoplasten. Aktuell werden solche Bauteile so verwendet, dass beide Komponenten zunächst separat gefertigt, zum abgelegenen Einsatzort transportiert und dort gemeinsam montiert werden. Dies verlangt jedoch eine umfassende Ersatzteilverfügbarkeit vor Ort. Das Team der Hochschule möchte dies ändern und ein Verfahren entwickeln, in dem beide Bauteile zugleich und direkt am Anwendungsort mit additiver Fertigung („3D-Druck“) hergestellt werden. Für die Entwicklung solcher Produkte sind zuvor jedoch komplexe Simulationen erforderlich, die am Labor für Maschinendynamik durchgeführt werden. Entscheidend für die Funktion der Dichtung ist der Schmierfilm, der sich zwischen Dichtung und Stange ausbildet und nur wenige Mikrometer dick ist. Er wird im Labor für Maschinendynamik mittels Elastohydrodynamischer (EHD) Simulation berechnet. Hierzu wird das nichtlineare elastische Verhalten der Dichtung einerseits und das Strömungsverhalten des flüssigen Schmierfilms (Reynoldsgleichung) andererseits modelliert. Diese Modelle werden zu einer Gesamtsimulation miteinander gekoppelt um die exakte Filmhöhe, die Druckverteilung und die Dichtwirkung zu berechnen. Die entstehende Finite-Elemente-Simulation wird in Comsol aufgebaut auf einer leistungsfähigen Workstation mittels GPU-Computing durchgeführt. Sie erlaubt es, Optimierungsrechnungen durchzuführen, um z.B. besonders geeignete Geometrien zu finden, die mit konventionellen Fertigungstechniken nicht möglich sind, sehr wohl jedoch mit additiver Fertigung.